
Richard Buckminster “Bucky” Fuller (July 12, 1895 – July 1, 1983) was an American architect, author, designer, futurist, inventor, and visionary.
Throughout his life, Fuller was concerned with the question "Does humanity have a chance to survive lastingly and successfully on planet Earth, and if so, how?" Considering himself an average individual without special monetary means or academic degree, he chose to devote his life to this question, trying to identify what he, as an individual, could do to improve humanity's condition, which large organizations, governments, and private enterprises inherently could not do.
Pursuing this lifelong experiment, Fuller wrote more than thirty books, coining and popularizing terms such as "Spaceship Earth", ephemeralization, and synergetics. He also worked in the development of numerous inventions, chiefly in the fields of design and architecture, the best known of which is the geodesic dome. Carbon molecules known as fullerenes or buckyballs were named for their resemblance to geodesic spheres. [...]
In The 1940’s Buckminster Fuller designed a utopian house that resembled a spacecraft. It embodied the American faith that technology, science and industry could solve social, and even, spiritual, problems.
There was tremendous demand for the Dymaxion House, but the start-up costs were high and Fuller was a notoriously bad businessman. In the end, a few were made by hand, but the project never fulfilled the promise implied by the mechanical reproducibility of the design. [architectureandhygiene.com]
The Dymaxion House was developed by inventor and architect Buckminster Fuller to address several perceived shortcomings with existing homebuilding techniques. Fuller designed several versions of the house at different times, but they were all factory manufactured kits, assembled on site, intended to be suitable for any site or environment and to use resources efficiently. One important design consideration was ease of shipment and assembly.
The word Dymaxion is a brand name that Fuller used for several of his inventions.
The Dymaxion was completed in 1929 and later redesigned in 1945. Buckminster Fuller began to investigate "Dymaxion" in 1927. He wanted to mass produce a bathroom and a house. His first "dymaxion" design was based on the design of a grain bin. During World War II, the U.S. Army commissioned Fuller to send these housing units to the Persian Gulf. [...]
Criticisms of the Dymaxion Houses include its supposed "one-size-fits-all" cookie-cutter approach to housing which completely disregarded local site and architectural idiom, and its use of energy-intensive materials such as aluminum rather than low-energy materials such as adobe or tile. Fuller chose aluminum for its light weight, high strength, and long-term durability, arguably factors that compensate for the initial production cost. Aluminum was also a logical choice if the homes were to be built in aircraft factories, which, since WWII had ended, had substantial excess capacity.
The Wichita House was a project Fuller took during WWII in trying to produce cost-effective dwelling for everyone. The project continued to develop the technological background of the concept behind the Dymaxion House, now incorporating a round floor plan instead of a hexagonal one. The reactions to the prototype were extraordinarily positive; nevertheless it was not put into industrial production. Fuller, a consummate perfectionist, felt he could improve the design and was dissatisfied with the prototype. He scuttled production rather than allowing the "unfinished" design to proceed.
Buckminster Fuller Institute
_____________________________________________
Prefabricated homes, often referred to as prefab homes, are dwellings manufactured off-site in advance, usually in standard sections that can be easily shipped and assembled. Some current prefab home designs include architectural details inspired by postmodernism or futurist architecture.
Prefab homes have not been particularly marketable; possible reasons for this include:
>Homes are not currently produced cost-effectively enough for current demand.
>Homes are not considered a realistic housing solution by the average consumer.
>The consumer is either not familiar with the concept, or does not desire it.
>Social stigma that exists because of low quality mass produced designs used in the past.
>Difficulties obtaining finance due to stricter guidelines being used by lenders to assess prefab home loans.
Recently, however, modern architects are experimenting more often with prefabrication as a means to deliver well-designed and mass-produced modern homes. Modern architecture forgoes referential decoration and instead features clean lines and open floor plans. Because of this, many feel modern architecture is better suited to benefit from prefabrication.[...]
In the United Kingdom the word "Prefab" is often associated with a specific type of prefabricated house built in large numbers after the Second World War as a temporary replacement for housing that had been destroyed by bombs, particularly in London. Despite the intention that these dwellings would be a strictly temporary measure, many remained inhabited for years and even decades after the end of the war. A small number are still in use in the 21st Century.
_____________________________________________
Modular homes are houses that are divided into multiple modules or sections which are manufactured in a remote facility and then delivered to their intended site of use. The modules are assembled into a single residential building using either a crane or trucks. [...]
Modular components are typically constructed within a large indoor facility on assembly lines much like Henry Ford originally instituted with his automobile company. Such facilities use an assembly line track to move the modules from one workstation to the next. Independent building inspectors are on site to supervise the construction and ensure that all building codes are adhered to during assembly.
Such dwellings are often priced lower than their site-built counterparts and are typically more cost-effective to builders and consumers. These new homes can be constructed in less time than it takes to build a home "on-site". Manufacturers cite the following reasons for the typically lower cost/price of these dwellings:
>Indoor construction. Assembly is independent of weather which increases work efficiency and avoids damaged building material.
>Favorable pricing from suppliers. Large-scale manufacturers can effectively bargain with suppliers for discounts on materials.
>Ability to service remote locations. Particularly in countries such as Australia there can be much higher costs to build a site-built house in a remote area or an area experiencing a construction boom such as mining towns. Modular homes can be built in major towns and sold to regional areas.
>Low waste. With the same plans being constantly built, the manufacturer has records of exactly what quantity of materials are needed for a given job. While waste from a site-built dwelling may typically fill several large dumpsters, waste from a modular dwelling generates much less waste.
_____________________________________________
Welcome to the fabprefab fablist where we present modernist prefab dwellings that
>are available for purchase in North America
>are actively marketed as a product/solution by a vendor
>have had a prototype or finished example of the dwelling constructed.
Also:
>The structure is a single family dwelling that could be used as a permanent residence.
>The design is "modernist" in form.
>A significant proportion of the dwelling is fabricated or assembled off-site.
_____________________________________________
Inhabitat's Top Ten Prefabs
_____________________________________________
Michelle Kaufmann Designs


In March 2004 we spoke to Michelle Kaufmann of MK Architecture about Glidehouse.
fabprefab: What motivated you to create Glidehouse?
MK: The project is the result of a frustrated and failed search for modern affordable housing in San Francisco. I had recently moved to San Francisco to join my husband after 6 months of a long-distance marriage. I was in LA working for Frank Gehry, Kevin was in SF, and we flew back and forth every weekend. When we finally decided to live in the same city, we wanted to find somewhere that could really be a home for us.
So began the most frustrating 6 months of my life searching for a house in the Bay Area. Sunday mornings racing around to open houses, always being disappointed by what was available and shocked by the prices. “$600,000 for a one bedroom fixer-upper!! Move fast! This deal won’t last!” We were just about to give up when we thought about the possibility of building a home. Once we made that decision,everything moved very quickly. We found a lot within a week. I started designing a small modern sustainable house. My husband Kevin kept questioning and pushing me to make the house as green as possible.
During the design process, we had a lot of interest from friends and colleagues. Our friends were saying that they wanted one too. “Can you do a modern, green house like that for us?” So, we started thinking about how that could happen. I started talking to many factories and modular builders to see about the possibility of making our house in quantity.
fpf: Did you hold a view that you were developing a product?
MK: Absolutely. As we worked through the details with the factories, we used our friends as a kind of litmus test. We tried to imagine what they would want in terms of process and product. I think the process is a big component. Our friends are young(-ish) people, who are quite busy with work, biking, snowboarding and starting to have kids. So, although many are in the design-related or green-related field in some way, they are too busy to go through the typical process of hiring an architect, designing a house, going through the permit process, finding a contractor, meeting weekly with the contractor and architect, dealing with hassles that can arise during the building process.
We therefore designed the process, as well as the product, to be as streamlined as possible. So, unless a buyer has a desire to be greatly involved (or has a brother who is a contractor), they can just make the critical choices in the beginning, and then sit back and have someone else complete the work until the house arrives.
Although we originally designed it for our friends, we found that many different types of people found the Glidehouse suited their needs – older people wanting to downsize and simplify their lives, people looking for a second home, people looking for an in-law unit for local parent care, or people who want to live as lightly on the land as possible. [...]
fpf: You are using a network of fabricators. How easy was that to organize and how complete is the network?
MK: Initially the majority of the factories were not interested in discussing any modern designs, but rather, were eager to offer up one of their colonial or faux-chateau designs. It took quite a while to find anyone who was willing to discuss making the Glidehouse, but eventually we found the right people in the modular world who had a similar vision. There has been a tremendous response to the Glidehouse and that helped us be able to find factories that see this as a viable investment. Currently we have coverage on the intermountain and coastal states of the West, Michigan, Ontario, BC, and are working on New York and other east coast states.
fpf: Are your fabricators content to produce on a piecemeal basis or do they need to see some volume for their numbers to really work?
MK: They have agreed to build them as the orders come in, but with more orders, there will be more savings.
fpf: You spent five years in Frank Gehry’s office. What projects were you working on there?
MK: While I worked with Frank, it was mainly on museums. This is one of my favorite building types – spaces of display. There were many things about designing museums that I now apply to residential work. Create clean spaces, control daylight at different times of the day, produce good lighting, but hide the lighting source, use clerestory windows to create a clean wash of light on the ceiling and space. One of my favorite museums is the Norton Simon museum in Pasadena. I love the way the gallery spaces connect to the sculpture gardens. This blurring of the interior and exterior is something I am also interested in with residential work.
fpf: Can you tell us about the materials you have chosen and why?
MK: The exterior siding is Cor-ten steel.
It has that warm velvet color and texture that looks contextual whether it is in the woods, in the desert, or in the middle of a neighborhood. There is no maintenance required, and it just keeps looking better over time. Sculptors, like my favorite – Richard Serra - have been using it for years. I enjoy watching people who can’t help but touch these pieces. I love the idea of a tactile house. Cor-ten is also a material I associate with home. I grew up in Iowa where there were a lot of beautiful rusted steel buildings.
Walls of Low-E sliding glass doors.
These maximize cross-ventilation, maximize natural lighting, maximize connection to the outdoors. Through the use of 8’ wide sliding louvered panels in front of the glass doors, one can customize the amount of daylight and shading depending on the time of day and year. The sliding louvered panels also can lock into place and provide security when the sliding glass doors remain open for constant breeze but homeowners are away or sleeping.
Galvalume metal roof.
Low maintenance. When solar panels are used, they blend in to the galvalume metal roof beautifully.
Bamboo flooring.
This is renewable wood. The strand woven bamboo uses the waste from other bamboo floorings and recycles it into a lovely textured wood floor that is quite durable.
Concrete countertops with recycled materials. Beautiful. Green. What more could you ask for?
Wood storage wall.
The storage wall allows a system for a lot of “stuff”, so the living space can remain clean and uncluttered. This system also allows people flexibility to customize their spaces depending on the kind of storage they put behind each door (e.g. literature, media, sports equipment) or they can leave open for display, or leave out to expand living space.
fpf: Your marketing materials make a statement about sustainable design. Can you tell us what this means to you?
MK: Sustainable design means a number of things to me.
Green living – minimizing the amount of energy used to build the house (modular manufacturing has very little waste) and also the use of renewable/recyclable materials. Also minimizing the amount of energy the homeowner will use while living in the house. For example using glass walls and panels to control temperature and shading, solar or geo-thermal where appropriate, using a proprietary Heating Recovery system that recycles 30% of the energy used during heating and cooling, Radiant heat flooring, using high r-values for insulation etc.
It also means healthy living – for example creating an environment that surpasses standards from the American Lung Association.
fpf: How does the financing process for modular homes differ from homes built on-site?
MK: It is slightly different, but no more difficult for the buyer as long as they know the banks that specialize in modular building. The rates are the same, down-payments and appraisals are the same as site-built. The draw system for payments to the factory vs. general contractor are what is different. We have a few banks that we recommend who specialize in modular lending and make it as simple as possible for the buyer. They can roll land and Glidehouse into one loan, can offset payments until the house is complete and so forth.

_____________________________________________
Marmol Radziner Prefab




In California, Leo Marmol and Ron Radziner have earned themselves a reputation as the go-to architects for dream homes and classic house renovations. As a measure of their credentials, consider this: they've now built six homes for Tom Ford and they were the retro-fit architects of choice for the new owners of Richard Neutra's legendary Kaufmann house.
It's a little surprising then to learn that Marmol-Radziner and Associates is quietly building a thriving side business in prefabricated homes. But lest you are overcome by images of clunky builds that threaten to collapse with a combination of bad weather and bad design, the Rincon homes (named after the iconic surf break north of LA) are studies in muscular minimalism.
'I think these days, the term prefab is thrown around wildly,' says Radziner. 'Our prefabs are modular and are delivered to site complete with everything in it.'
Rincon 5, as the current range is known, is 60-ft long and barely distinguishable from a site-build, so meticulous are the detailing and construction standards. The $220,000 fee includes construction costs. Radziner points out that each Rincon takes eight weeks to build in the factory and is delivered to the site complete with tiles, plumbing and even fixtures like dishwashers and sinks.
Architects have in general been enthusiastic about prefab homes (well, those designed by Marmol-Radziner at least) lauding them for their sustainability, cost, time efficiency and eco-friendliness. The downside, of course, is economies of scale. It will be some time yet before the prefab arm is in a position to produce ready-builds en masse let alone to the standard that Radziner expects.
In the meantime, the firm is busy with traditionally built homes in California and Seattle, with a childcare centre for Disney thrown into the mix. [Wallpaper.com - Nov.08]
In October 2005 we spoke to Marmol Radziner Prefab about their new Steel Homes product line.
fabprefab: When did Marmol Radziner + Associates start planning a prefab product line?
MRP: For nearly a decade the firm has been using prefabricated steel structures in our institutional projects, most notably in the LAX First Flight child care center and The Accelerated School in South Los Angeles. In both cases, prefab modules offered simple, quick and affordable solutions that still matched the modern aesthetic of the buildings.
Then in 2002, we were invited to be part of the Dwell Home competition, and for the first time we applied prefab technologies to a residential project. We were so enthusiastic about the potentials of prefab homes, that soon after we began designing a prefab prototype. Building the prototype, which we call the Desert House, helped us learn more about the realities of prefabricating homes, and the three models we currently offer are based on what we discovered with the Desert House.
MR+A has a reputation for high-end projects and attention to detail. Can you tell us how the values of your firm might be reflected in your new products?
MRP: Marmol Radziner Prefab is a natural extension of our firm’s long-standing approach that combines design and construction to produce modern spaces that are designed and built with exacting detail. We are architects first and foremost, and we see construction and fabrication as the work that supports our designs because it allows us to bring the rigor that we used in designing a project and to apply it to the construction process. Because we fabricate and handle all aspects of our work, we are responsible for everything we build and can ensure a high level of detail and quality for the homes. Our custom site-built homes have always focused on indoor/outdoor living, and we have carried that ideal into our prefab homes as well. The material selection, open floor plans, and floor-to-ceiling windows all reinforce this modern ideal. [...]
Marmol Radziner Prefab
Amid the industrial expanse of Vernon, California, Marmol Radziner Prefab’s factory-built homes are pieced together in a process akin to the assembly lines made famous by Henry Ford.
Making Green Modular Homes with LA Architect Marmol Radziner (vid)
_____________________________________________
In 2002 Dwell Magazine hosted the Dwell Home Design Invitational. This competition, for a modern prefab prototype home designed for mass production, was won by Resolution: 4 Architecture. The Dwell Home /Wieler Residence was built for clients Ingrid Tung and Nathan Wieler in Pittsboro, North Carolina and was unveiled to the public on July 10 2004.



_____________________________________________
If you've been listening to the chatter on prefab and thought: "What's the big deal with prefab homes?" or "Why would anyone ever want to own a prefab?", now's your chance to find out. In his most recent update from A Prefab Project, Chris dropped a link to his shiny new website for lostrivermodern, a prefab cabin in Lost River, West Virginia. And as you can tell from the images on the new website, lostrivermodern is quite incredible to look at. Designed by Resolution: 4 Architecture, creators of the original Dwell Home, lostrivermodern is the first and only res4 home available for guests. You can (and probably should) rent the place and completely chill out. I see some slots are already filled up, so if you're interested in testing the prefab waters on the East Coast, you better get on it quick.
Chris has kept a pretty good tally of his actual and estimated costs for Lost River Modern -- not to mention allowing us in to watch and learn from the process. lostrivermodern is a plus $350k project and worth every penny I would say. [jetsongreen.com]



_____________________________________________
FlatPak






Q & A with Charlie Lazor of FlatPak
[prefabs.com - May.08]
Charlie Lazor, a practical and determined young designer, is the creator and principal architect of FlatPak, a modern prefab home design and manufacture firm in Minneapolis, Minnesota. His vision for prefab housing is heavily influenced by his design and manufacture experience as a co-founder of Blu Dot Furniture. I interviewed Mr. Lazor at his current home, the original FlatPak house, in Minneapolis, Minnesota.
Company: FlatPak, Minneapolis, MN
Education: B.A., Williams College; Master of Architecture, Yale University
Prefabs: Your Professional Background?
Charlie Lazor: I finished architecture school in 1993 and started practice. I was just getting my feet wet in architecture and learning about not only designing buildings, but how to communicate with builders, and how to get things done. This was a pretty big shift from architecture school and making drawings, where nuts and bolts are not part of the experience.
Prefabs: And how did you get involved with Blu Dot Furniture?
Charlie Lazor: My friend, my college roommate, John Cristakos, had an idea of starting a design and furniture manufacture company. The idea was that we would design it, manufacture it and act as the seller of the furniture to retailers. I moved to Minneapolis and we started 11 years ago this weekend -- the anniversary of the International Contemporary Furniture Fair in New York. We took our first prototypes to New York, and set up a booth, put out our wares and waited for people to come. It was kind of fun. At the end of the weekend we instantly had this business and a stack of orders -- but no product, no packaging, no forms, no warehouse, no forklift, no pallet racking… [Laughing]
It was a lot of fun. It just kind of took off and it seemed like we hit a chord with this idea of accessible furniture design. It was accessible in that there's a reason for why it looked like it did; it was functional, it was straight-forward, it was simple, and it was pretty reasonably priced and available at retail shops. It’s kind of amazing to think that when we started there was not a Design Within Reach, no Conran Shop -- it was still very much a place of expensive, contract kind of furniture world. The designers and architects had access to the showrooms, but the general public did not. We were interested in the general public. The general public could buy our stuff, take it home, and put it together.
Prefabs: Interesting that many great architects were also furniture designers.
Charlie Lazor: Yeah. I think we are very much in the area of the form making business -- the result of observation, sometimes research and often times just iteration of getting a form right, so that it works and that it makes sense. And that it's legible. Not only legible in what it is, but in how it’s put together. It's very much a built to made thing. There has been a long history of that.
The irony is that when I was in school in the late 80's and early 90's, I don't think that was of much interest at all. That was a period of designers like Eames, Marcel Breuer, Walter Gropius, Buckminster Fuller, The Case Study Program, it was really... it was history. It wasn't still alive and wasn't a touch point for most people in architecture school. When I was in school, it was a lot more about narratives and fictions and it was very much about the kind of things that would cut against the pragmatic, humanist approach to design.
Prefabs: At some point you left Blu Dot, was that because of your interest in prefab?
Charlie Lazor: It was primarily because of my interest in architecture. I had always intended that I would give three to five years to building Blu Dot and then get back into architecture.
But the move back into architecture took this specific approach of looking at prefabrication as a way to make houses and deliver houses and also design houses -- that was very much an extension of what we were doing at Blu Dot, scaled up in the size of the project.
Furniture doesn't have plumbing or electrical, heating or air conditioning in it -- and it stays inside -- it doesn't need to keep the water out. So, it’s a comparatively complex problem but it's basically a similar kind of thinking process -- it just works on a different scale.
Prefabs: And you to started FlatPak about this time?
Charlie Lazor: Yes. It’s kind of funny, I remember designing things at Blu Dot -- I would always put myself inside the furniture, inside the letter holder, or the magazine rack and thought of them as architectural spaces or propositions. I was really just dying to make buildings again.
What was interesting to me at Blu Dot though, was that I learned about another way of thinking about making. When you're an architect, you're trained as an architect, you practice as an architect, there's a culture in the profession of architecture about how you do things. It’s pretty specific and it’s pretty narrow.
But furniture design that I did at Blu Dot was about manufacturing. We were interested in manufacturing. You have such a high degree of control over what you get. The dimensions are right, holes are in the right place and the finish is what you asked for. You have a much greater command over the material product. Whereas architecture, you give a large set of drawings to a contractor, and they give it to a subcontractor and they give it to someone lower. It’s a game of telephone, involving very large sums of money. Not fun.
FlatPak was, for me, a way to keep my sanity as an architect, because I need things to be very precisely done, and competently and carefully done. I need a lot of control to do that, so the manufacturing methodology made a lot of sense to me. Why is Lazor Office doing prefab? There is a whole series of reasons, but one of them is merely a way to practice and keep my sanity. [Laughing]
Prefabs: Where would you say you are at in the whole scheme at FlatPak?
Charlie Lazor: Step one was the designing and building of this house, the FlatPak prototype [his current home]. It was completed in the summer of 2004. Step two, we licensed the fabrication, marketing and the sales to a company called Empyrean*, a component based builder of modern houses. This November [2007] I took FlatPak back into my office to do everything under one roof.
We designed and built about a dozen FlatPaks across the country, but I wanted to grow FlatPak in a different way, meaning integrated in marketing, sales, design, fabrication and assembly. So our core FlatPak team has developed FlatPak ‘2.0.’
Prefabs: Prefab companies seem focused on design, are there bigger problems?
Charlie Lazor: Only a segment of it [Prefab] is an "architect or designers" problem, and then the rest of it is all the entities required to make it successful. There is a sales and communication function. There's a design function, obviously. And, there's a fulfillment function.
We have a fulfillment system which is going to be based on a team of assemblers who do all the jobs. Everyone that gets a FlatPak house gets the same team, with the same FlatPak jumpsuit and super hero capes on, jumping out of the FlatPak truck to put their house together.
I feel that is a big jump forward for us. The knowledge base required is embedded with the doers, as opposed to trying to embed the knowledge with different crews as you go. We're really excited. We have some great consultants and a robust team that is experienced as well as a bend to doing things in progressive but practical way.
The consultants that we have on board are pushing the envelope in their respective areas. The building industry, particularly residential, is very fragmented, and it’s very stubborn and very conservative. It’s an industry that doesn't change.
What we are doing, in my mind is obvious. The problem is it goes against the grain of how things are and so that makes it more of a challenge. You're not going to get it right the first time out. I think the ones that are persistent and who are flexible and listen well are the ones who will succeed. I'm confident that we will be in a good place in the next couple years.
Prefabs: After living in the FlatPak prototype, are there things you changed in the FlatPak design?
Charlie Lazor: The outside of the house is very much like our current houses with some small material substitutions. On the inside, we've spent a ton of time fine tuning details, but the essential idea of eight foot panels that can be tiled together starting at the roof and working down to a variable height has stayed the same.
One thing that has changed from this house as a prototype is the window system. The prototype had glass directly mounted to the frame of the house. We now use a conventional, commercial grade aluminum window and door system. The ceilings, the cabinetry, the concrete floors, radiant heat, the wall dividers and the sort of a plug and play system of material choices, remain the same.
Prefabs: So a few things have changed?
Charlie Lazor: Yeah. It’s not so much the design and the material, it’s been developing methodologies for communicating to the clients what FlatPak is and developing methodologies and tools to communicate with the client during the design process. And the same process of developing methodologies to document and make decisions in the office and how we communicate that to the crew that is putting it together. To me, this is what is often missing with Prefab, it’s like four fifths of the problem.
Yes, you need a system that is logical and makes sense, a system that works on a module, but to me that's a fifth of the problem. A lot of it is industrial engineering type prefabs questions that don't often get baked into the idea.
Prefabs: Prefab often seems misunderstood by consumers…
Charlie Lazor: The prefab house has been over simplified in the media. Like a lot of things, it sounds too good to be true, and it is. A lot of people think these houses show up with a ribbon around them, lifted onto the foundation and two days later you’re living in it. The amount of work that happens before all that is tremendous. I think a lot of people were writing about prefab a few years ago as some kind of miracle solution. They are not low cost housing, they do not happen instantaneously.
Prefabs: Your idea of success in building a FlatPak home?
Charlie Lazor: Our goal is to build these houses in less than six months and provide as much value to our clients as we can.
Prefabs: And in terms of FlatPak as a company, your idea of success?
Charlie Lazor: I'm a true believer in building a business slowly and carefully, learning to crawl before we walk, and walk before we run.
My goal is to do about a dozen houses in the next 12 months. Based on that, I would be pleased if we did about two dozen homes a year after that. Most of all, each home is a client; a person, or a couple. We want them to be happy and fulfilled with their FlatPak house and to say it was a great experience.
*Empyrean is currently in a State Court Receivership.
___________________________________________
LivingHomes
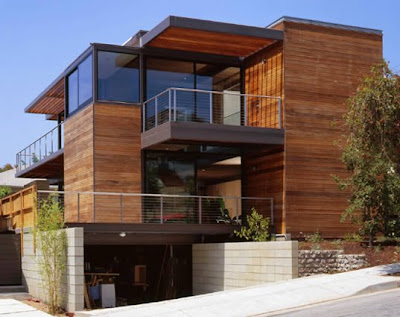

The Living Home prototype (above) is designed by Ray Kappe, an award winning architect and educator in Southern California.
In 1972, after three -and-a-half successful years as professor and Founding Chairman of the Department of Architecture at California Polytechnic State University, Pomona, Ray Kappe resigned. With a group of faculty members and students, he started the Southern California Institute of Architecture (SCI-Arc). The SCI-Arc model of education encourages learning through creative discourse and supports diversity of opinion within the framework of a common vision. Today the school is 34 years old, with 3,000 graduates working and teaching all over the world. It is considered one of the top architecture schools in the country.
As of 2007, Kappe is still actively involved in architectural theory and practice, particularly in the areas of sustainability and the prefabrication of residences. [Wikipedia.org / LivingHomes.net]
Architecture of Ray Kappe - slideshow
Greenest House in America (vid)
The 2,480-square-foot home is 80% more energy efficient than a conventional structure of similar size.
It cost $390 per square foot to build, some 25% less than typical high-end construction in the neighbourhood.
(Owner Steve) Glenn's monthly power bill: $10
CEO Steve Glenn & architect Ray Kappe (vid)
Ray Kappe: All my work expresses honesty of structure and honesty of material.
Steve Glenn: Homes built traditional ways are extremely wasteful...the industry needs to be transformed.
SG: The insulation we use in the walls is from Bonded Logic. It's 100% denim (and) not treated with any weird chemicals.
___________________________________________

American House 08



American House 08, is the first in a series of ten prefabricated houses designed and constructed by William E. Massie — the award-winning Architect-in-Residence and Head of the Architecture Department at Cranbrook Academy of Art.
American House 08 embodies Massie’s drastically divergent practice from traditional architecture through his use of computer-based fabrication technology for efficient, precise, and customized fabrication. Constructed entirely within the architect’s 12,000 square-foot studio just minutes away from the historic Saarinen-designed Cranbrook campus, American House 08 was designed, in part, at full scale. By composing in real-time, Massie is able to negotiate between material and concept, relying on human reaction to the actual space and details. Utilizing computer-based fabrication technology for production, the house consists of a prefabricated steel frame, in-filled with manufactured structural panels all filtered through a process of digital fabrication.
American House 08 Intro by William Massie (vid)
Massie Produced
[Dwell - Feb.09]
William Massie always longed to live, work, and build in the same place. For most of his career, the charismatic architect, known for championing the latest design technologies, had to travel long distances in order to construct his experimental homes.
Then, in 2005, after becoming head of the architecture department at the Cranbrook Academy of Art in Bloomfield Hills, Michigan, Massie had less time to do even that. Shortly after relocating for the job, he came across a former tool-and-die factory that was for sale in nearby Pontiac. At 10,000 square feet, it was large enough to erect a house in. Massie snapped it up. Finally, he could work on his residential designs close to home and in his own time.
Last summer, the architect completed the first home to come off of his factory’s highly idiosyncratic production line. An all-white, superbly elegant, 2,500-square-foot modernist box, the steel-framed house, which was built in sections, is easily recognizable for its roof line that parabolically plunges at one point to form a dimple.
The house, which Massie dubbed the American House 08, was built to move: No sooner was it completed than the architect jumped behind the wheel of his dual-axle GMC truck and towed many of its components five miles along Woodward Avenue to Cranbrook. The house was reassembled on a lawn outside the art museum, next to a towering sculpture by Mark DiSuvero. After the addition of cork flooring and newly plastered ceilings, the house, part of an exhibition on Massie’s work, was opened to the public. But the 08 still faces a much longer and yet to be determined journey: to its eventual client.
For Massie, creating this “transportable” house proved inspirational. “It is the culmination of everything—the digital technology, the prefabrication techniques, and more formal architecture—that I have brought to my designs,” he states. Walking inside, it is clear why. Massie’s grasp of domestic space, honed by a reverence for early modernists like Richard Neutra and Rudolf Schindler—he once lived in a Neutra house in Bozeman, Montana—has been enhanced by the freedom that designing inside his factory allows.
At first, all he did was erect the steel frame. Abandoning the standard practice of deciding a house’s layout before construction, Massie spent hours walking around inside to figure out, from the occupant’s point of view, what it would be like to live there. “There was never a need to finalize beforehand where the bathroom wall should be or where the front door had to be placed,” he recalls. For the first time in his career, Massie found himself free of demanding clients. “They are not good coconspirators,” this obsessive experimenter confesses. And experiment he did. Sometimes his search for different materials meant roaming up and down the aisles of Lowe’s and Home Depot, both equidistant from his factory, on his Segway. At other times, he would simply sit in a chair and see that a certain window could be higher. “I was able to play constantly,” the 46-year-old exults.
The result of this approach (Massie refers to it as “subtly improvisational”) is an interior that responds immediately, albeit quietly, to an occupant’s needs. Massie lowered the ceiling, creating space between the ceiling and the roof and making the house feel less like a solid block. He then made sure that the views from the master bedroom both to the living area and to the outside spoke directly to the choices offered by the house: Is it time to go outside to the lawn or return to the main space?
Some decisions were straightforward. In keeping with modernist tradition, skylights and floor-to-ceiling windows in the living room invite natural light inside; the question for Massie, as he wandered around inside his frame of a house, was simply how to use that light. He soon decided that shade, even darkness, would make the master suite feel more separate, so he inserted a 34-foot-long panel to bisect the wall of glass. The darkened room thus feels apart from the rest of the house and, appropriately to Massie’s original idea, more private.
When Massie attended Columbia University back in the late 1980s, he and his classmates believed that the computer would revolutionize design. For many, that ended up meaning greater dexterity with programs like AutoCAD. Massie, however, was determined to use this new technology in the construction process itself, not merely as a design tool.
For over a decade, attaching his computer to a laser cutter, he learned how to draw intricate shapes—such as jigsaw patterns for wood paneling—and have the machine cut them out seamlessly. He then bought his own computer numerically controlled (CNC) milling machine, which could drill down into a material to create molds. He was thus able to redefine how standard materials such as concrete, wood, and even rubber were used. They no longer had to be flat or rectangular—they could become sculptural forms.
As soon as one steps inside the 08, the results of these battle-tested skills are evident. Two sculpted pods dominate the living room. One is the reverse of the roof dimple while the other houses a large stand-alone bath and shower. Both are made from the same structural insulated panels (SIPs) that in-fill the exterior, but, thanks to the laser cutter, these panels were sliced into even smaller pieces and pushed into dramatic shapes.
Massie’s computer-design wizardry is not confined to grandiose gestures. The cabinets—which look like thin sponges—are simply whiteboard sculpted out by the laser cutter according to a pattern set up on the computer (when viewed at the right vantage point the varying ellipses all condense to form perfect circles). In the master suite, two small rectangular sections of the walls have been filled with translucent rubber cubes also cut on this machine. “They allow light through as well as some exciting shadowy movement,” Massie says.
Sometimes there seems no end to these flourishes. Orange rubber molds fill in the elliptical recesses on the house’s solid end walls; from certain angles the torqued shapes flatten out to form perfect circles. The bathroom sinks are made from the same colorful material. Surprisingly, though, the house does not feel self-conscious. “I don’t like design to be fetishized,” he says flatly.
The 08 seems to amplify Massie’s own freewheeling spirit. During my visit he invited friends and family in for drinks. A built-in projector shone an episode of Twin Peaks onto the wall of the sculptured shower pod. LEDs in the floor beamed different colors onto each side of the dimple. With the rest of the living room subtly lit, it became a New York cocktail lounge. Those inside soon forgot, if they ever knew that what they were sitting in had been prefabricated in sections, transported to the site, and then bolted one to the other. Of course, this is the way Massie wants it. This architect came to the idea of transportability to satisfy his own design ambitions, not because he was obsessed with prefab.
When the house is moved again, some interior surfaces, such as the plaster ceilings, will, in Massie’s words, “have to be sacrificed.” Redoing them, and reinstalling the floor, will cost about $20,000. The total transport cost, apart from any work to connect the house to the site, will be nearly $45,000. The cost of the house itself? $750,000. But the new owner will be getting something unlike any other prefab: a one-of-a-kind house by William Massie.
The architect is asking the buyer to view the 08 as a work of art. To that end, he has contemplated putting it up for auction on eBay. Like many of Massie’s ideas, this seems outlandish. Then again, so did buying an abandoned factory in suburban Detroit. The architect would have it no other way.
___________________________________________
Perrinepod
Perrine



Since Jean-mic Perrine first talked about the Perrinepod, the Perth architect has been inundated with inquiries from all over the world. As a result, the release of the first pods was delayed to make sure they would comply with various international codes. The pod comes with a Solar Edwards Heat Pump hot water system that uses refrigeration technology in reverse to heat the water. A small electric booster motor can be powered by a solar cell for the complete environmental package.
The pre-cast concrete sections of the pod are manufactured in the shipbuilding precinct of Henderson by French engineer Serge Picoult’s company Accue which usually builds concrete sections for wharves and other big industrial projects. [cubeme.com]
Perrinepod can be built in 3 days and withstand everything from earthquakes to cyclones. It's not only durable, but green in its material, systems, and long life-span...additionally, Perrinepods can be stacked on top of each other (up to 30 units tall!) to create larger complexes.
When talking about green residences, the discussion often centers around materiality (what’s it made of?) and systems (how is it powered?). The Perrinepod is a good example of green-ness in durability, as its sheer heft and strong walls (made from pre-cast, pre-stressed and tensioned concrete with an R value of 6.8- a typical brick-and-tile house with insulation is R1.9) mean it’s probably not falling apart or going anywhere anytime soon.
If you’re wondering about more traditional green features, the Perrinepod has a high-tech solar system available that powers the home as well as heating water. Additionally, the high-grade concrete provides superior insulation for both hot and cold months.
As for the pricetag, the one-bedroom version, which weighs in at a hefty 114 tons, starts at $125,000, while a three-bedroom, two-bathroom pod starts at $250,000. [inhabitat.com]
COMMENTS
[inhabitat.com]
Disaster proof? Sitting that low to the ground and with all that glass? Looks to me like it wouldn’t hold up in a flood, hurricane, hail storm or tornado. A tornado would break all the glass and suck the insides out! Sure, the concrete would still be standing, but you’d have to completely start over on the interior. Does still having a shell left standing after a storm really qualify it as being distaster proof?
A quick look at the corporate website shows that this firm is based in Australia - and the prices are AU only. We have investigated purchasing one of these for our new home, and have found that, despite the obvious advantages of prefab, the units can also be cast onsite in remote locations.
A number of the photos on their site are for a real house that has been established [you can see the building site through the windows].
As for ‘disaster proof’ - it probably wouldn’t withstand a nuclear blast either. C’mon people - if you were living in an area prone to different types of weather you could either do the smart thing and move elsewhere or adapt the design to suit your requirements.
I imagine a nice set of heavy duty hurricane shutters that could be locked into place across exposed glass would solve the problem.
And a shell is a better place to start building from than nothing I would think, but hey, that’s just me.
__________________________________________
Taliesin Mod.Fab


You’ve never seen a school project like this – Mod.fab is an amazing modern prefab house designed by students at Taliesin West, in conjunction with Jennifer Siegal and Victor Sidy. Designed for sustainable living in the desert, this one-bedroom, 600-sq.-ft. house features panelled construction that allows for off-site assembly – a big bonus both economically and environmentally speaking. This prefab house incorporates a variety of innovative eco-friendly features in this “unplugged” design, including low-consumption fixtures, rainwater harvesting technologies, greywater recycling, natural ventilation, solar orientation, and photovoltaics to reduce energy and water use, all to minimize environmental impact while providing a stylish and secure lifestyle. The Mod.fab house is on display on the student-led Taliesin West Desert Shelter Tour until April 25, 2009. [trendir.com]
___________________________________________
ContainerBay
There is growing interest in the use of shipping containers as the basis for habitable structures. These "icons of globalization" are relatively inexpensive, structurally sound and in abundant supply. Although, in raw form, containers are dark windowless boxes (which might place them at odds with some of the tenets of modernist design...) they can be highly customizable modular elements of a larger structure.
Shipping Containers Recycled as Homes (vid)
Last year (2005) seven million containers arrived here full of imported goods but only 2.5 million left carrying American exports; many of the rest are polluting residential areas near the ports.
DeMaria Design Associates
Awards
Bank of Manhattan - Innovative Entrepreneur of the Year Award
LA.Curbed - 2008 Building of the Year Award
American Institute of Architecture - Excellence in Design - Innovation Award
First Prize - City of Inglewood Parks and Rec Design Competition
w/ Long Beach ACE Academy/M. Brookman
Best of Show Distinction - CES 2008 - EM Magazine
AIA Young Architects Forum - Professional Service Award
Metal Architecture National Award
First Prize Award - RAND Corporation Competition
AIA/LA - Educator of the Year Award

The traditional design, permit and construction process, compounded by skyrocketing construction costs, has necessitated a re-birth of the design/build approach to creating architecture. Like the work produced by the Master Builders of centuries past, this project is a direct result of the architect’s re-insertion into the building design process and the method by which the project is constructed. A by-product of the architect’s total immersion into alternative construction methodologies is the employment of reinterpreted building components.
This project is a recycled steel shipping container based building that also employs a combination of conventional stick frame construction and prefabricated assemblies. These materials result in an end product that is affordable and nearly indestructable. The modified containers are mold proof, fire proof, termite proof, structurally superior to wood framing and along with various other “components” come together to create a system/kit of parts that is predicated on cost savings, construction timesavings, and energy/environmentally conscious priorities. Seventy percent of the building is efficiently created/assembled in a controlled shop environment where quality construction and fabrication are the highest priority.
The Redondo Beach House has been completed and it received the 2007 AIA Honor Award for Design Excellence/Special Innovation. This project has given birth to a new residential product line. It's what we call Packaged Architecture™. This line of homes will launch in 2008 through our affiliate Logical Homes (below).

Still Playing with the Box
[LA Times - Jul.06]
Anna and Sven Pirkl wanted a house built around their eclectic, athletic lives. What they are getting may be a blueprint for future unconventional homes that just might rock suburbia.
At first glance, it looks like a mix-up on the docks of San Pedro. Eight shipping containers — those orange-, green- and rust-colored boxes that truckers haul on L.A. freeways — sit stacked two high at different angles on a lot in Redondo Beach. The steel containers, now painted white, have windows, door openings and some entire sides cut out. But there's no disguising their cargo-carrying heritage.
They make up different wings of a contemporary-style house that will have a 20-foot-high living room and two walls of airplane-hangar doors that will open completely to the outdoors.
"We wanted something different." says Anna Pirkl, a 34-year-old artist, who is building the house with her husband, Sven, 37. "We wanted something contemporary and modern. But it was getting more and more expensive to do what we wanted to do."
The structure is eye-catching in its oddity, a standout in a suburban neighborhood of single-story tract houses and recently remodeled two-story homes. By using containers for much of their house, the Pirkls say they are saving a bundle.
Dozens of architects have explored using the strong, weatherproof, steel containers to create inexpensive, environmentally responsible housing. Container-based dwellings have been an option for at least a decade, and have turned up as youth hostels in South Africa, field hospitals in Jamaica, art studios in London and dormitories in Amsterdam.
In the United States, a handful of completed projects include a few highly original container-based residences in New Jersey and New England by Adam Kalkin (below), an off-beat architect and performance artist. In architecturally adventurous Southern California, Jennifer Siegal designed the SeaTrain House in an industrial area of downtown L.A. using containers as part of the structure.
For Anna and Sven, the container idea started as a joke.
About eight years ago, the couple saw a lot for sale but they only had money to buy the lot.
"So I joked with Sven," says Anna, " 'We should just go down to Long Beach, grab a couple of those shipping containers, weld 'em together, put in a few windows' … I was just kidding. With building prices the way they were — and are — we just couldn't find a way to build the house we wanted."
After they acquired the Redondo Beach property, she checked prefab houses on the Web. "I contacted all kinds of metal companies, to see if they wanted to do something new and cool on our lot. But nothing was really clicking."
Then the couple was introduced to Manhattan Beach architect Peter DeMaria, unaware that he too had been interested in containers.
"We didn't mention anything about containers," Anna says, "but we told him we wanted to be as environmentally sound as possible, to do any recycling we could. We wanted our house to be low maintenance. We wanted it to be as creative as possible. And it had to fit our budget."
Early in the architect's pitch a couple of weeks later, the Pirkls figured out that he was suggesting containers. "And we said, 'Fine.'
"I think Peter was a little disappointed that we said yes so fast — he'd worked hard to create this great, elaborate show, and he didn't even get to finish it."
"Beyond using the containers," says the irrepressible Anna, "we have a number of things we're doing inside the house that are going to be a lot of fun. Like this," she says, pointing to an interior side wall of the 20-foot-high living room where there will be a climbing wall.
"Sven and I are sports fanatics. We're going to put a zip line —a tight steel cable —down a hallway, so you can reach up, grab the handles, and ride to the next room. We'll probably also put in some swings, some gymnastic rings. Those are the kinds of things we like to do. We figured, why wait 'til you go to the gym or go off on a weekend or a vacation to do that sort of thing?"
"There are certain expected activities that take place in a standard house," says architect DeMaria. "But this house is a more interactive experience than any other I've been involved with. The house enables Anna and Sven to do the things that are unique to them: hang on that zip line, climb that wall, ride their mountain bikes up the front ramp and through the wide-open living room, in one side and out the other.
"Stylistically, we had no preconceived view of what the building should look like," DeMaria says. "We knew we wanted it to function for them. We started to arrange things to support what they wanted to do. I'd like to think that the building reflects them, and the way they like to live … At one point we were going to put a half-pipe in the back yard."
Four of the largest containers sit perpendicular to the street above a concrete garage, two stacked on the right, two on the left. The lower boxes will serve as hallways and open-air porches, the upper one on the left will be the master bath and walk-in closet, the one on the upper right will house a library-guestroom.
In between is a two-story frame structure, which will contain Anna's art studio on the first floor and the master bedroom above. Four smaller, 20-foot containers, joined to the rear of the right-side front containers, will house the kitchen and utility room on the first floor and two guest rooms on the second. Behind the kitchen is the living room, a 20-foot-high, steel girder and wood frame cube. All of the containers came from Florida where they were specifically modified for the Pirkls' project.
"I wanted to feel as if I was outside," says Anna, "especially in the living room, where I was going to spend most of my hours." The architect originally planned to use roll-up garage doors there, so the whole house merges with the environment.
"The living room would become our entire backyard," says Anna. "Then he found these airplane-hangar doors, which fold out instead of rolling up. And they're actually better, because you still get the light coming in from the windows above the doors, and if it rains, we can keep them open — because when they're folded up, they extend out to form a kind of awning."
When all the bills are totaled, the Pirkls hope to complete their, 3,500-square-foot, four-bedroom, 3 1/2 -bath home for $125 a square foot — half of the $250-$270 average for custom building in the area.
DeMaria, his associate, Christian Kienapfel, and the Pirkls concentrated on reducing cost without reducing content. Using the containers for over half of the house's structure yielded major savings. The container sections will have no internal or external sheathing. Anna and Sven decided they liked the look of the painted, corrugated container walls just the way they are, even with their original dents.
Insulation is provided by an innovative, NASA-developed ceramic coating, a little thicker than a credit card, sprayed on the interior and the exterior surfaces.
As in many South Bay homes, their house will not have air conditioning. To reduce maintenance to a minimum, durable, automotive-style acrylic paint has been sprayed over the insulation. The Pirkls see no reason to cover the original, industrial-strength wooden container floors. Electrical fixtures and conduit run unadorned throughout the house, with most electrical outlets built into the container floors.
"Over and over again," says DeMaria, "we're taking materials from other industries, reinterpreting or reapplying them to this scenario, and we come up with a reinvigorated thing, something with a fresh feeling to it.
"Those hangar doors work better for what the Pirkls wanted to do. And they're also much less expensive than residential doors. It's hard to get a door that's 20 feet wide and 18 feet tall. That door's normally going to cost $35,000. We're doing two of them here, for a quarter of the price."
The main stairway to the second floor will be enclosed in a translucent box of lightweight acrylic panels, usually found in greenhouses. Precisely finished, formaldehyde-free plywood will be used to form internal walls and partitions, and to lend some warmth to counteract the industrial look of the containers' walls. Prefabricated concrete-board sheets will sheath the climbing wall, saving labor and maintenance costs.
The Pirkls had hoped to be living in their new house by now, but delays in obtaining permits and in construction have pushed their move-in date to mid-August.
With their previous house already sold, the Pirkls need a place to store their furniture and belongings. The solution is simple —and one fully in keeping with the philosophy of reusing industrial castoffs to create innovative, entertaining forms.
One more used, 40-foot container has been delivered to the backyard to shelter their possessions until the house is done. They will then dig a hole in the yard, cut the top off the container, drop the container into the hole, and fill it with water. Voilá: an instant lap pool.
Sven and Anna's housewarming party is likely to be a memorable affair. Guests will be advised to dress casually. To wear their bathing suits. And to bring their climbing shoes.

COMMENT
[la.curbed.com - May.07]
About the house... love it or hate it, new technology like this prompts dialogue about recycling, alternatives to the status quo, affordability of construction, and esthetics. Non-Architects/neighbors are discussing progressive ideas regarding "what should a residence be?" That, in and of itself, makes me want to support this project. It looks like a serious piece of Architecture, not some whimsical stuff you would find on Melrose Ave. The jury is still out and only time will tell. Apparantly other folks/clients believe in what the Architect is doing. Where is the ground breaking???
I assume that the Redondo project had some headaches when it came to timing and inspections, maybe more than a typical wood structure, but anything that is forward thinking is always scrutinized to the max. I've lived through a remodel and the building dept. is very demanding. In reality, __ (who sounds like he is frothing at the mouth) represents a percentage of the public out there who complain about things that are simply "different".
No one likes new construction sites next to their property but when its completed, they all love the increased value that it brings to their neighborhood. In the USA, folks are resistant to change... until they see the financial benefits. At that point, all of the criticized, battered and "crazy" ideas are referred to as "innovation" that changes the way we live.
If this doesn't convince you, go to Wikipedia.org and look up Prius. Adios!
Logical Homes

Fifty years ago it was assumed that by now we would all be living in space stations high above the earth. Yet the future didn't quite work out that way. Most of us live on terra firma in homes that (in the rich western world) are built pretty much the same way as those constructed fifty years ago: by people standing out in the sun hammering wood together.
At Logical Homes we strive to design homes that are appropriate for the era we live in. We challenge traditional notions of what a house looks like, how it is built, what it is made of and how it performs. Our designs incorporate recycled and repurposed industrial materials. Our homes are not high-tech; we like to think of them as appropriate-tech: always designed with an understanding of the materials and technologies that surround us and with a respect for the scarcity of resources our planet faces.
We believe that the options available to progressive homebuyers are limited and we have chosen to do something about it. Our homes are by no means for everyone. If you are seeking a Tudor-themed tract home then you are looking in the wrong place. However if you are not afraid of new ideas and you're looking for a well-built modern home then we just might be able to help you.
Logical Homes Officially Launched
G Living Talks to Peter DeMaria About Container Design and Sustainability
QUOTES
(As an architect) you have to understand that dollars have to come from somewhere.
Last year (2007) 65 million tons of demolition material was transported to the dump - that is a shocking number.
You've got to bring to people all the solutions before they ask the questions and that's what we've done, both from a political standpoint and from an engineering standpoint and that's why we've had success with it.
We're calling it "Next Generation Prefab".
People have asked me "Why have you done this?", and it's all about being a good leader in the profession.
Once you show someone a different light there's a strong chance they'll grab on to it if it's a good idea.
____________________________________________
Container City - official site


Shipping Container Homes by Container City
Enough shipping containers exist on our planet to build an 8 foot high wall around the equator - twice.
A container's final destination is usually the scrap yard.
The cheapest form of construction is an existing box.
A total of 100 units make up Container City I...a 300-square-foot space - the size of one container - costs about $80 to $140 / month to rent.
Container Condo to be Built in Detroit
A 17-unit condominium built from shipping containers is being proposed for Detroit, on lots now vacant or containing burned-out homes. According to the Detroit Free Press, "The project would stack empty containers four high, cut in windows and doors, install plumbing, stairways and heating, and add amenities such as balconies and landscaped patios."
COMMENTS
[treehugger.com - May.08]
As a resident of the city of Detroit, I am very delighted a project of this scope is going forward. Detroit is a complex and exciting place to live - something which cannot be conveyed on realtor.com.
Seems like a great idea for rebuilding New Orleans. The bottom level could be open, or used for parking to prevent flood damage.
I own a large commercial wood framing company specializing in apartment and condo projects and have given much consideration and thought to modifying containers for upscale apartments, condos, student housing, and prefab single family homes. Some very cool and creative spaces can be created if you just think out side of the "BOX". There are many ways to stack them, cut them and open large areas inside so you dont feel so cramped. Additionally finishing the outside would be rather easy if so desired. You can even make pitched roofs with large overhangs to shade the lower walls from the sun. The list goes on and on with some creative thinking.
It's important to ensure a second-hand container was not used to ship noxious goods, or has anything like formaldehyde residues.
These are ideal for Detroit... they're bulletproof.
Architecture and Hygiene



The 12 Container House is a custom prefabricated house created by architect and artist Adam Kalkin from 12 recycled shipping containers. This "T-shaped" 2-story summer home features floor to ceiling windows, concrete floors, two fireplaces and radiant in-floor heating.
It's available for rent June - October for $6,000-10,000/week
Adam Kalkin - CNN Highlight (vid)
QUOTE
Any orthodox point of view makes me very uncomfortable.
Containing a Home: Adam Kalkin '84
The cargo containers, with a life span of about 20 years when used for their original purpose, have an “infinite life span” when stationary and properly maintained, Kalkin says. Giving these formerly mobile containers a permanent home as homes means that despite providing the structure for a brand-new house, each container comes with its own ready-made and traveled history. “You can look at them both as junk or as something special,” Kalkin notes. “To me they are like a treasured antique: they may not be inherently valuable, but the history and the storytelling add value.” Kalkin’s inventive architectural vision grows directly out of his belief in interconnectedness. He argues, “We come from a culture of sampling. I’m just out there in the world picking out things and reusing things—sampling—from my experience and from what other people have already invested a lot of time and energy in. I think there’s a tremendous amount of richness out there.”
His ability to mix unlikely sources and materials with the fairly straightforward domain of domestic architecture sets him apart from other architects, he thinks: “I’m a little bit outside of architecture, in the sense of my lack of allegiance to a specific kind of behavior or orthodoxy. I don’t value architecture culture over other cultures: I draw from writers, music, and the visual arts. Who wants to narrow the world down?” Instead Kalkin hopes he’s “seeing real connections between things and reaching toward a humanitarian core,” revealing that the “distinctions we’ve built up are false ones.” Just as insects make the most of a fallen tree in a forest, utilizing the tree for both shelter and food, Kalkin sees the sense in “repurposing” objects for architectural ends. Or, as he says, “Any kind of junk can be turned into stuff.” [...]
While Kalkin admits that once he designs something and releases it into the world he doesn’t mind who takes up the design or what exactly they do with it, he does resist associations between his purpose and specific causes. “Sometimes there’s a natural alliance between me and the environmentalist world. However, whenever you get orthodox about something, you lose your conceptual playfulness. You then have a framework, and, ultimately, you become boring. There is a humanitarian core to what I’m doing, but I also don’t want to feel like I’m too serious and totally in service to other people.” [...]
Kalkin has recently made the important decision of maintaining control over his house. Left with the choice either to license his designs or begin to manufacture the products himself, he’s opened a factory—“a hangar at a little airport in New Jersey”—to do just that. “I need to own the product,” he says. “There are a lot of elbows flying in this process, and this is the best way to protect the quality of the house, to keep the accounting transparent, and to make sure I am not unwittingly responsible for heinous crimes to the built environment.” Once the factory is fully functional, Kalkin plans to export many of his products, commenting that “the possibilities of working on a world scale are exciting.” [...]
Amazing Homes and Offices Built from Shipping Containers - slideshow

Billed as the largest container city in the world, Amsterdam's massive Keetwonen complex houses 1,000 students, many of whom are happy to secure housing in the city's tight real estate market. Designed by Tempo Housing in 2006, Keetwonen is said to be a roaring success, with units that are well insulated, surprisingly quiet and comfortable.
Each resident enjoys a balcony, bathroom, kitchen, separate sleeping and studying rooms and large windows. The complex has central heating and high speed Internet, as well as dedicated bike parking.
Keetwonen has proved so popular that its lease has been extended until at least 2016.
Shipping Container Housing: Are the Floors Toxic?